OPTICAL 3D PROFILOMETERTM
- Home
- Industry
- OPTICAL 3D PROFILOMETERTM
OPTICAL 3D PROFILOMETERTM
NOVACAMTM OPTICAL 3D PROFILOMETERTM system is fiber-based and provides:
Micron-precision 3D measurements
- Dimensional geometry – GD&T parameters
- Roughness measurement
- Defect detection – cracks, scratches
- Thickness measurement of semi-transparent materials
Option to scan even hard-to-reach surfaces:
Side-looking probe scans inside bore IDs and other tight spaces, forward-looking probe is also available
Fiber-based probes that are easy to integrate with precision stages, third-party CMMs, CNC machines, or robots to support high-volume continuous flow manufacturing
Fully configurable automated inspection.
Notably the same probe can be used to measure dimensions, roughness, defects, and/or thickness.
Product Specifications :
Overview
Application
Software
Additional Info
FAQ
Overview
Overview of features and benefits
Measurements
- Optical, non-contact, non-destructive
- High speed: Up to 100,000 3D point measurements per second
- Micron resolution, excellent S/N ratio
- 2D and 3D surface and subsurface characterization
- Dimensions, roughness, defects, thickness
- Long stroke profilometry
Imaging
- Surface profiles
- Cross-sections
- Volumetric images
Fiber-based probes
- Inspect inside bores, tubes, and crevices
- Provide versatility for high-speed online inspection
Benefits
- Wide range of materials: metal, plastics, polymers, glass, metal coatings, silicone, adhesives; reflective, transparent, semi-transparent, specular, nonspecular
- Wide range of surfaces: measured objects can be stationary or moving, solid or liquid, and include interiors of bores and tubes, exteriors of cylinders, concave or convex spherical shapes
- Small-diameter probes reach in to measure insides of bores and small-diameter tubes
- Measures high-aspect-ratio features: undercuts, cross-holes, chamfers, rifling, threads, O-ring grooves, and edges
- Reduced inspection cycle time: up to 100,000 measurements per second, each representing a 3D topographic point
- Versatility of setup: Non-contact probes work up to 1 m away from surface and several meters from the interferometer
- Continuous, long profile scanning: no area stitching required
- Flexible options for evaluating inspected parts: measured features can be compared to CAD drawings or to a user-defined set of locations, nominals, and tolerances
- Simple scan definition and execution: The scanning sequence is defined once by teaching the system with a joystick. The scanning sequence can later be executed with the push of a button.
- Time-saving automated reporting: Following a scan, go-no-go reports can be produced, and results logged in a manner compatible with industry-standard mechanisms
- Easily integrated in lab, shop, or fully-automated inspection setups: probes may be mounted on XY tables, on multi-axes scanning mechanisms, inside machining centers, above moving webs, on robot heads, etc.
- Adaptable to hostile environments: radioactive, very hot, cryogenic, vacuum, etc.
- No consumables are needed: Optical probes do not come in contact with the measured samples, and therefore do not wear out like contact probes
- USB connection for data transfer from interferometer to PC or laptop
- Option of multiplexing several probes with single interferometer for additional return on investment (ROI)
Application
Metrology Applications
Typical measurements
- Dimensional measurements: geometric dimensioning and tolerancing (GD&T) parameters
- Thickness: single-layer or multilayer films, coatings
- Surface roughness: surface characterization, flatness, and more
- Volume loss: component wear or other damage
- High-aspect-ratio features: steps, holes, grooves, channels
- Hard-to-reach spaces: interiors of bores, small aperture tubes, etc.
- Profilometry in hostile environments: radioactive, cryogenic, very hot
- Long stroke profiles
- Thickness of non-transparent materials
3D metrology and imaging for industry and R&D
- Quality control
- Online 3D production inspection, GD&T
- Statistical process control SPC
- R&D
Examples of applications
- Electronics industry: geometry measurements of CMP pad grooves, glass edge and thickness measurement, wafer geometry
- Aerospace: jet engine turbine vanes
- Automotive: drive shafts, axles, threads, splines, gears, drive teeth
- Medical instruments sector: tubes, implant shaft interiors, optical cross-sections of intra-ocular lenses
- Biomedical and chemical sectors: vials, IDs of cylindrical containers
- Defence industry: barrels, bores, reamers, mandrels, drill bits, die blocks
- Tubular parts in high-precision machining, drilling, injection molding, 3D printing, additive manufacturing, casting, extrusion dies
Software
System Software
The OPTICAL 3D PROFILOMETER system comes with NOVACAM high-performance data acquisition software, which is PC Windows ® -based and user-friendly for scan programming.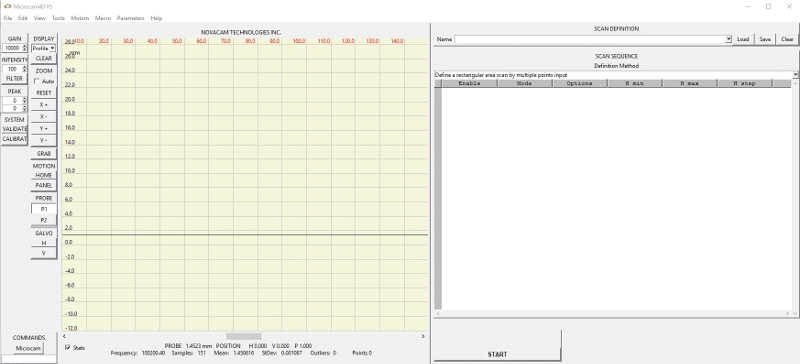
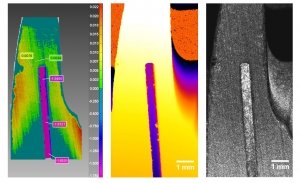
- Go-no-go reporting is easily programmed and automated.
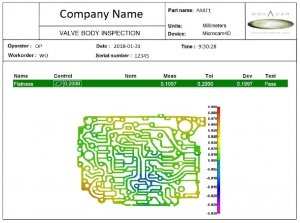
- Users benefit from capabilities such as a quick visual comparison (deviation map) of the acquired part measurements to pre-specified tolerances or to the CAD of the part.
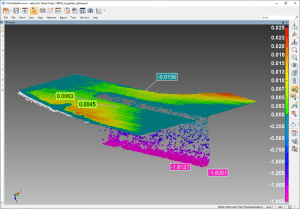
Additional Info
Standard system configuration
A standard configuration of the OPTICAL 3D PROFILOMETER system includes:- MICROCAM-3D interferometer
- Choice of
- 1 standard ⌀17.8 mm forward-looking probe
- OR
- 1 standard ⌀4.6 mm side-looking probe (for ID up to 300 mm (12″) deep)
- 2-axis inspection station and 2-axis motion controller
- Manual adjustment of probe height
- PC with NOVACAM acquisition software
- 1 year warranty
Instrument safety
- MICROCAM systems feature an in-probe red laser pointer (650 nm wavelength) for alignment purposes.
- MICROCAM systems are Class 1M Laser products, with < 20 mW of infrared and < 5 mW of in-probe laser pointer.
FAQ
What is the advantage of using a non-contact vs. contact profilometer for roughness measurement?
- Non-contact roughness measurements systems offer important advantages over contact measurement systems:
-
- no risk of affecting the surfaces as frequently happens with contact probe styluses
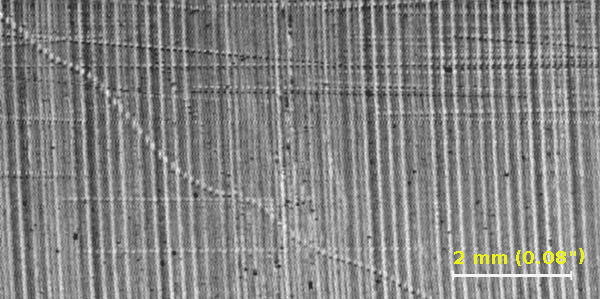
-
- no need for expensive consumables – optical probes do not get used up in the process of measuring
- no need for costly stoppages to exchange worn out contact probes.
- Yes. The scanning sequence (recipe) can be programmed with a joystick and can be recalled at later times with the push of a button.
- Yes. The system is ideally suited to both lab and shop floor inspection. Inline and robot setups are an option. The non-contact probes can even be configured to work in hostile environments such as extremely hot, cryogenic, or radioactive.
- Yes.
- Yes, depending on the geometry of the features to be scanned. Various curved surfaces and high-aspect ratio features have been scanned. Displacement stages can be added to the setup if required.
- Yes, if the coating is semi-transparent to infrared light and has optical thickness of 20 µm or higher (optical thickness = physical thickness * index of refraction).